Everything You Need to Know About SB 721 – California's Balcony Inspection Law
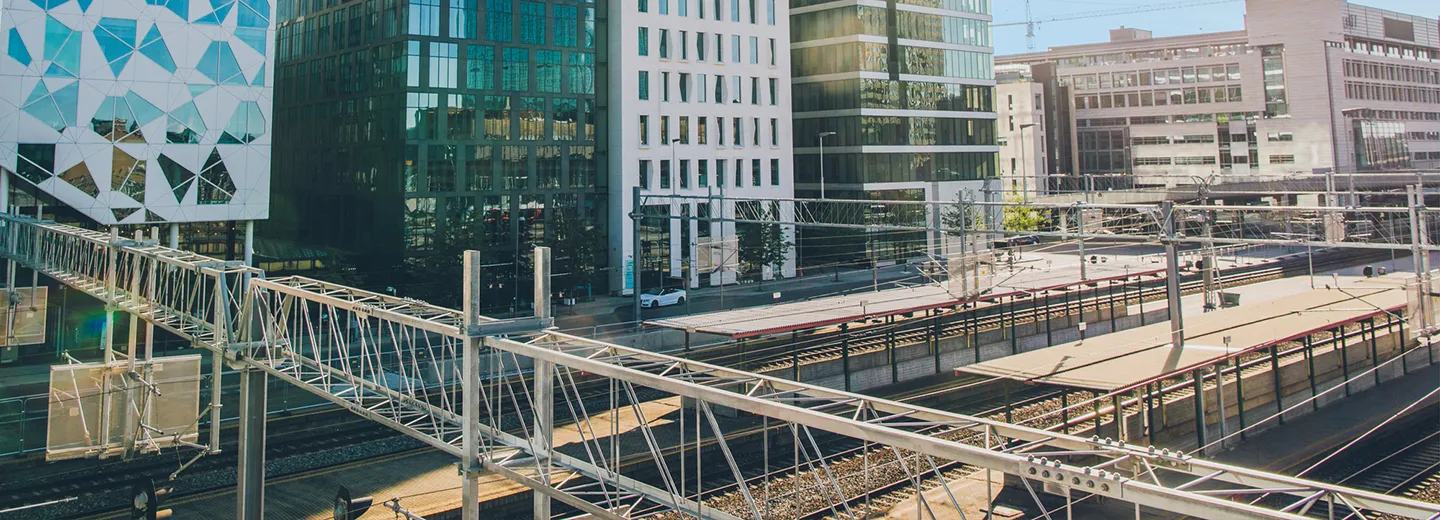
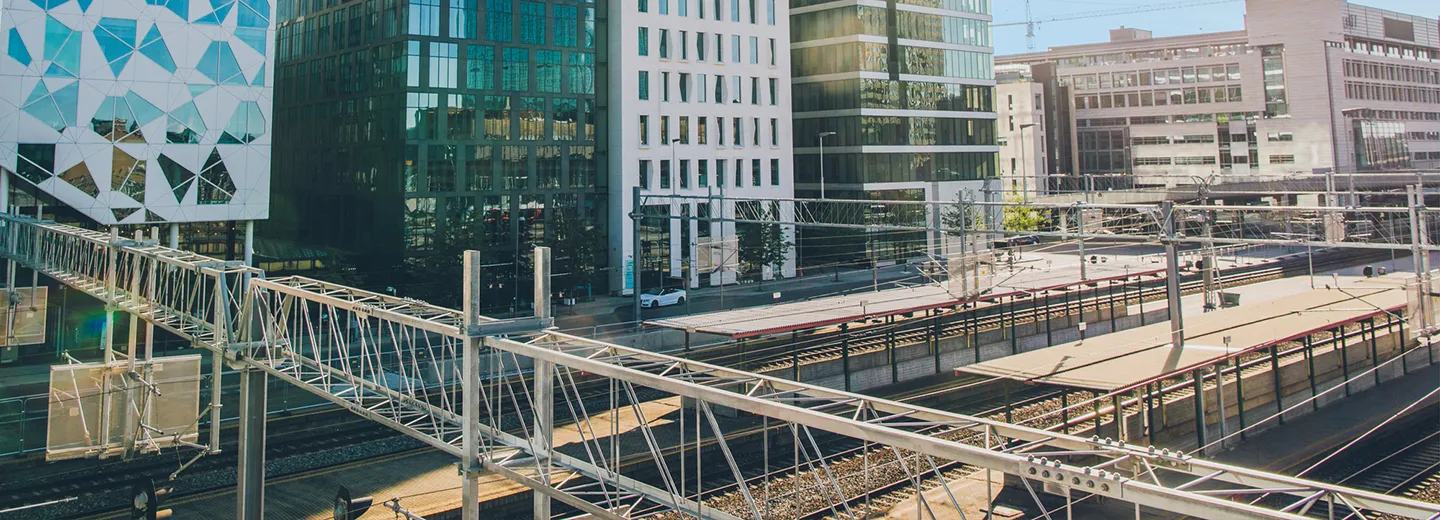
Balconies are a beloved feature of many homes and buildings, offering a space to relax and enjoy the outdoors. However, they also require regular inspections to remain safe and structurally sound. This blog post delves into the critical aspects of balcony inspections, focusing on wood components and waterproofing elements and the latest standards and technologies used in the process.
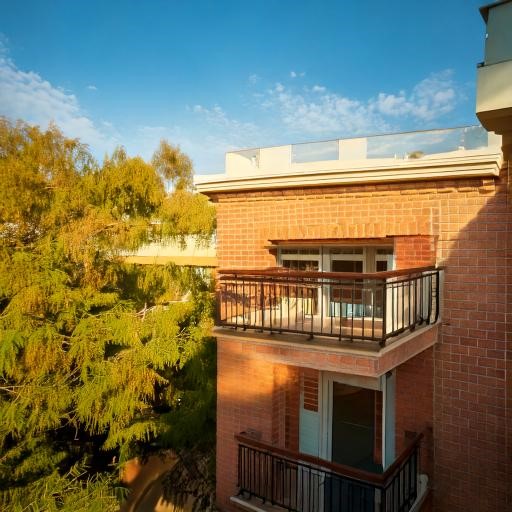
On June 16, 2015, a balcony at the Library Gardens apartment complex in Berkeley, California, collapsed, killing six people and injuring seven others. In their report on the balcony collapse, the California Contractors State Licensing Board concluded that the balcony collapsed due to dry rot damage caused by the contractor's use of inferior materials.
The jury awarded over $12,000,000 to the victims of the fall against the property manager and landlord who negligently maintained the residential deck that collapsed.
This collapse set into motion SB 721, a mandate that all exterior elevated elements that meet the criteria outlined below be inspected and have any necessary improvements performed.
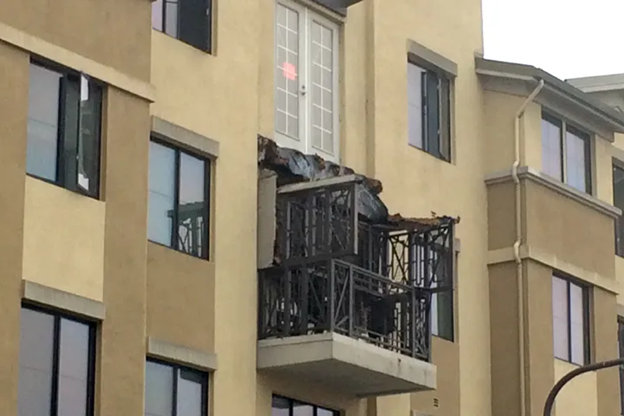
Understanding the Law: California Senate Bill 721 (SB 721)
- SB 721 (2018): This bill was signed into law in 2018 and took effect in January 2019. This law applies to buildings with 3 or more multi-family dwelling units and mandates that owners or landlords ensure a qualified professional inspects their balconies. The inspection must cover at least 15% of each type of exterior elevated elements (EEEs) supported by wood.
- Bill AB 2579, approved by California's governor on September 28, 2024, extended the deadline for the initial balcony inspection in California from January 1, 2025, to January 1, 2026. This extension is intended to help owners and operators with trouble completing inspections on time.
- To perform SB 721 inspections in California, a qualified inspector must be one of the following:
A licensed architect
A licensed civil or structural engineer
A building contractor with a minimum of five years of experience and a license classification of "A," "B," or "C-5" from the Contractors' State License Board
A certified building inspector or building official
- SB 721 inspections are required for decks, balconies, and other exterior elevated structures supported by wood in multi-family residential units. The inspections are intended to:
Prevent accidents caused by structural failures
Ensure the safety of residents
Address structural integrity, flashings, and waterproofing
The inspections are to be performed every six years
If a property was inspected within three years of January 1, 2019, a new inspection will not be required until January 1, 2026
Key Terminology Related to Balcony Inspections
- Exterior Elevated Element (EEE): Includes balconies, decks, porches, stairways, and walkways at least 6 ft. above ground level that extend beyond the building’s exterior walls and are designed for human occupancy or use.
- Balconies, decks, porches, stairways, walkways, and entry structures (including supports and railings) that extend beyond the exterior walls of the building and include walking surfaces.
- The walking surfaces are elevated more than six feet above ground level.
- The exterior elevated elements rely entirely or substantially on wood or wood-based products for structural support or stability.
- Load-bearing Components: Wood elements that deliver structural loads from EEEs to the building.
- Associated Waterproofing Elements: Flashings, membranes, coatings, and sealants that protect EEEs from water exposure.
Balcony Inspection Checklist
The inspector will evaluate the adequacy, condition, and performance of load-bearing components and their associated waterproofing systems regarding all kinds of EEEs, focusing on flashings, waterproofing, connections, and structural integrity.
Here’s a brief breakdown of what an inspector will look for during a formal balcony inspection:
- Improper or loose connections: The inspector will check for poorly connected EEEs, building framing, or wobbly railings that may collapse or cause accidents if someone leans on them.
- Metal corrosion and wood decay: Over time, moisture and chlorides can cause metal connectors and fasteners to corrode. Corrosion weakens fasteners and can cause surrounding wood to deteriorate, so inspectors will check carefully for signs of metal corrosion, dry rot, and deterioration of wood components that could render the balcony unstable or unsafe.
- Flashing / caulking issues: Moisture intrusion is the most critical reason for dry rot and structural failure of an EEE. Flashing / caulking are barriers that prevent unwanted moisture intrusion into the unprotected wood components.
- Cracks in load-bearing components: The inspector will also check for any obvious cracks or wear in decking material and signs of moisture intrusion and damage in deck surfaces and other load-bearing components.
The inspector issues a report of the inspection findings and photographic evidence to document the condition of all named EEEs and establish a historical record.
Inspection Methods and Technologies
To ensure thorough inspections, a variety of methods and technologies are employed:
- Visual Inspection
- Borescope: Allows inspectors to check for potential damage in elements/areas obstructed from view.
- Moisture Sensor: Measures moisture levels to detect water damage.
- Thermal Camera: Identifies areas of potential water intrusion by detecting temperature variations.
- Ultrasonic Metal Thickness Gauge: Evaluates the remaining thickness and corrosion of metal components.
Condition Category
- Immediate action required: The inspector finds an issue that poses a significant safety risk. This includes notifying local building departments and owners within 15 days and preventing occupant access to the affected areas. Repairs must be carried out promptly, and the area re-inspected to ensure safety.
- Repairs required: The inspected element is not functioning properly and requires repair as soon as possible.
- Maintenance required: Maintenance is required, but the issue does not currently present a safety risk.
- No problems found: The element is functioning as intended, considering normal wear and tear.
Penalties for Non-Compliance
- Fines: Up to $500 per day for non-compliance
- Safety liens: Local jurisdictions can issue safety liens against non-compliant facilities
- Enforcement costs: Local enforcement agencies can recover enforcement costs from property owners, landlords, and property managers
- Insurance: Insurance companies may raise premiums or deny coverage to properties with a history of non-compliance
- Liability: Property owners can face legal action and substantial liability costs if an accident occurs on a non-compliant balcony
Regular balcony inspections are crucial for maintaining the safety and longevity of these structures. By adhering to standards like SB 721 and employing advanced inspection technologies, we can ensure that balconies remain safe for occupants to enjoy.
About the Author:
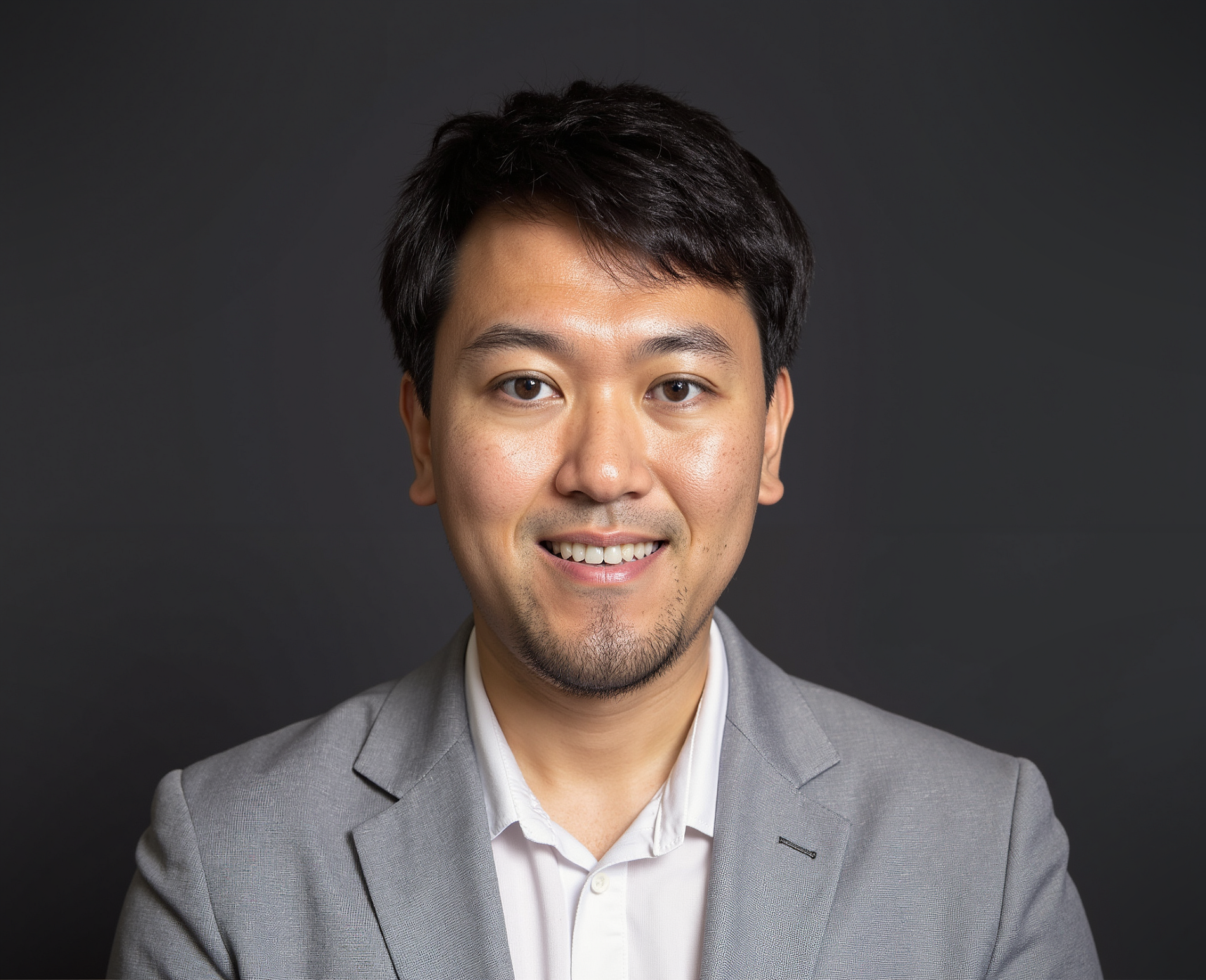
Xiaomeng (George) Ge, Ph.D., P.E., Senior Condition Evaluation Engineer
Dr. Ge (George) has an engineering background of over 16 years, performing design and investigation on a wide range of materials and project types. Although currently focusing primarily on investigative engineering and repair design, Dr. Ge also has significant experience designing new projects. Dr. Ge performs forensic site visual investigation and testing to determine the causes of failure.