Mind the Gap: Effective Stormwater Project Manager
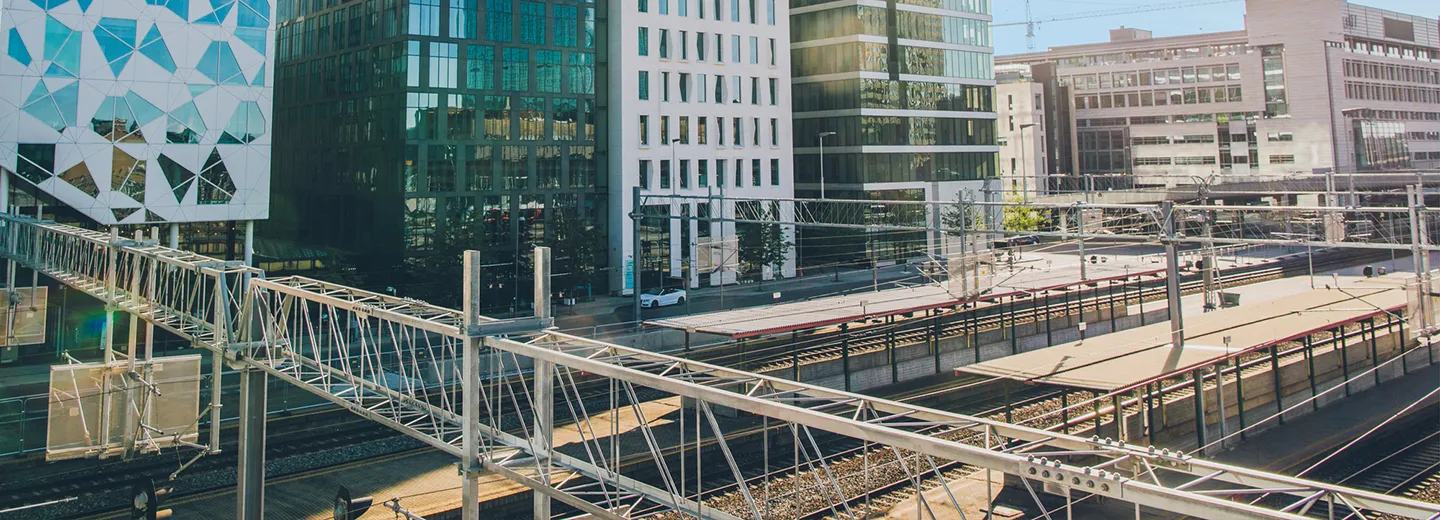
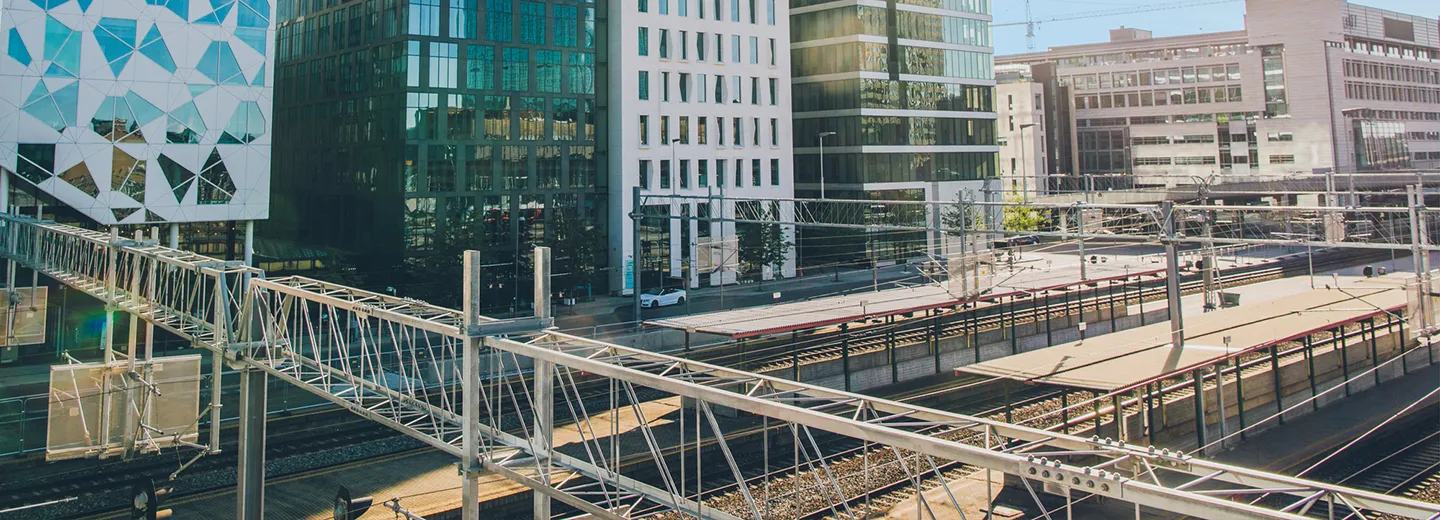
Twining’s Stormwater Manager, Milas Smith, wrote the following article for WTS. To view the article on their site click here.
A Little History
The phrase “mind the gap” was coined in 1968 in the London Underground for a planned automated announcement after terrible accidents and fatalities occurred because of slips and falls between the rail car and platform. Because some platforms on the rail line are curved, and the rolling stock or rail cars that use them are straight, an unsafe gap was created when a train stopped at a curved platform. It had become impractical for drivers and station attendants to warn passengers of the gap hence the “mind the gap” campaign. Mind the gap is now used worldwide in dozens of transportation systems and dozens of languages. The message simple and clear can be applied to Stormwater Management.
How Does “Mind the Gap” Apply to Stormwater?
Fortunately, there are a lot of smart people working hard to achieve the State of California and its Regional Water Control Board’s (RWCB) mission, which is “To preserve, enhance, and restore the quality of California’s water resources and drinking water for the protection of the environment, public health, and all beneficial uses, and to ensure proper water resource allocation and efficient use, for the benefit of present and future generations.”
Gaps in Stormwater Management
The problem lies in the gaps between the creation of the Erosion and Sediment Control Plan, subsequent Storm Water Pollution Prevention Plan (SWPPP), and boots in-the-dirt implementation. From the project owner aka “Legally Responsible Party” (LRP) or financier deciding to go forward with a project, to the Qualified SWPPP Practitioner (QSP) in the field performing the weekly inspection, there are some 15 or more gaps or transitions of implementation responsibility. Each one creates a small gap of lost intent, lost efficiency, and increased liability.
In the beginning the gaps are small. For example, the LRP of a project places all stormwater management, erosion and sediment control, and SWPPP responsibility on the engineering firm. Typically at this level, a Professional Engineer (PE) for the engineering firm is acting as a Qualified SWPPP Developer (QSD) while also preparing the project’s other various plans and drawings. The firm is also then retained to file the Notice of Intent (NOI) and obtain the state permit via the RWCB. If you glance quickly at this transition you can easily miss it, but the first gap has been created. The LRP has just created the first gap between the LRP and the project. In this example of the Construction General Permit (CGP), the intent is to keep the Owner and stormwater monitoring and environmental best practices closely tied together. In fact, per the CGP, violations are set up so that they are assessed directly back to the LRP. In most cases, the first gap is that the LRP doesn’t know what a SWPPP is, where it is filed, who it is filed with, what is contained within it, or that a subsequent permit is even issued with an estimated beginning and end date.
The Gaps Multiply Exponentially
Right away, the gaps begin and increase in width and depth from the first scenario described above. Of course, not all LRPs are uninformed of the state’s stormwater management requirements. Many LRPs know they are supposed to certify a plethora of stormwater documents throughout the course of the project.
As the project progresses, the erosion and sediment control plan and SWPPP move through the City’s permitting process. Then they move to the Construction Manager, the General Contractor, and finally to the QSP tasked with responsibilities of the SWPPP implementation. As the project moves through these various phases and on to construction, the baton of responsibility for the SWPPP implementation and monitoring gets passed from party to party. Gaps are created from the LRP to the QSD down to the project site QSP. This dilutes the original intent of the Construction General Permit.
Real Project Example
In the example image to the right, you can see the effects of gaps in terms of wasted time and money. This project is a flat parcel, 2-down, 5-up hotel, with approximately 1,700 linear feet of project perimeter. Just to left is the pit, leaving 2 feet of exposed soil around the perimeter of the project. On the other side of the wind screen fence is fully intact curb and gutter. What is wrong with this picture? To start, 5 Best Management Practices (BMPs) are not needed to protect this project from discharging sediment. Additionally, the BMPs are not installed correctly; the silt fence is backwards.
Why are there gaps, how do we mind them?
Quite simply, we go back to the original intent of the permit. The LRP, QSD, and QSP should be in close and continual communication. The QSP working for or on behalf of the LRP should be monitoring, managing, and making certain the SWPPP is being implemented in the most efficient way possible. In most cases, this cannot be accomplished by the CM, GC, or an all in one firm self performing these activities. A subsequent intent of the CGP is to avoid the fox guarding the hen house.
When a SWPPP is implemented correctly everyone wins. Money is saved by not wasting resources. Time and money is saved in project efficiency. Money is made by avoiding fines, project delays, and project shut downs. This method is not to be feared or even resisted. Again, the intent, the purpose, the motivation is “to preserve, enhance, and restore the quality of California’s water.
Milas E. Smith, M.B.A., CPESC, QSD, QSP, is a Certified Professional in Erosion and Sediment Control, Qualified SWPPP Developer, and Qualified SWPPP Practitioner. His education includes degrees from Cal State Northridge College of Science and Mathematics and Pepperdine University Graziadio School of Business Management. As Manger of Twining Stormwater, Mr. Smith oversees a team of Project Manger QSPs on projects ranging from Risk level 1-3, for Linear Underground, Construction General Permit and Industrial General Permit sites.