UT (UIltrasonic Testing) Reject in That Weld? Not So Fast…
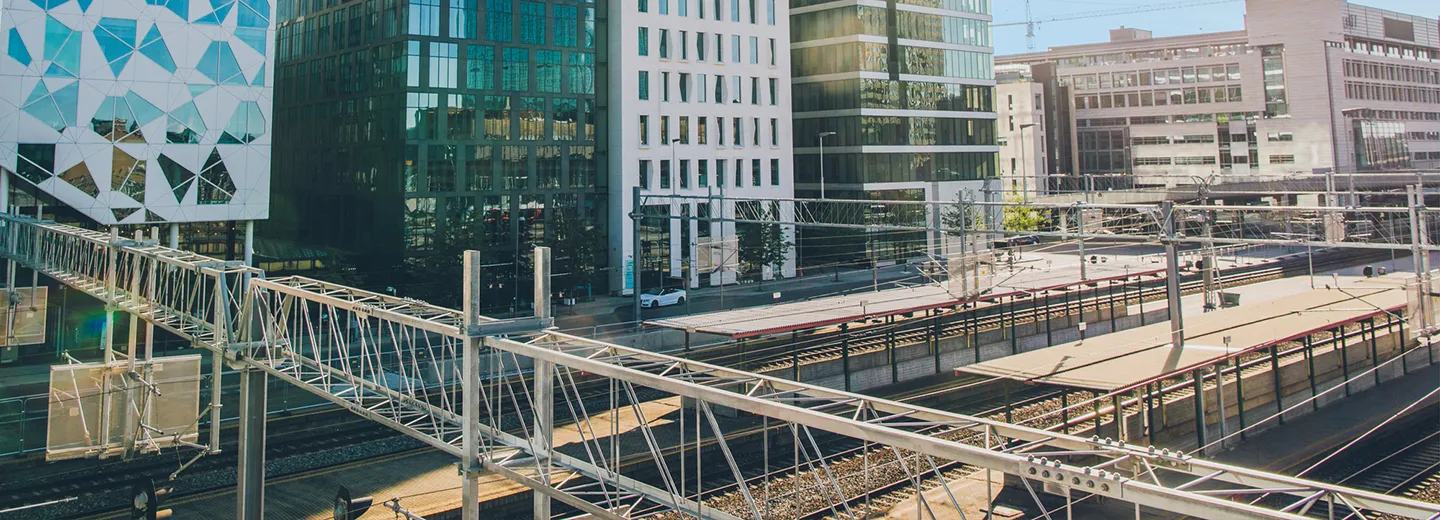
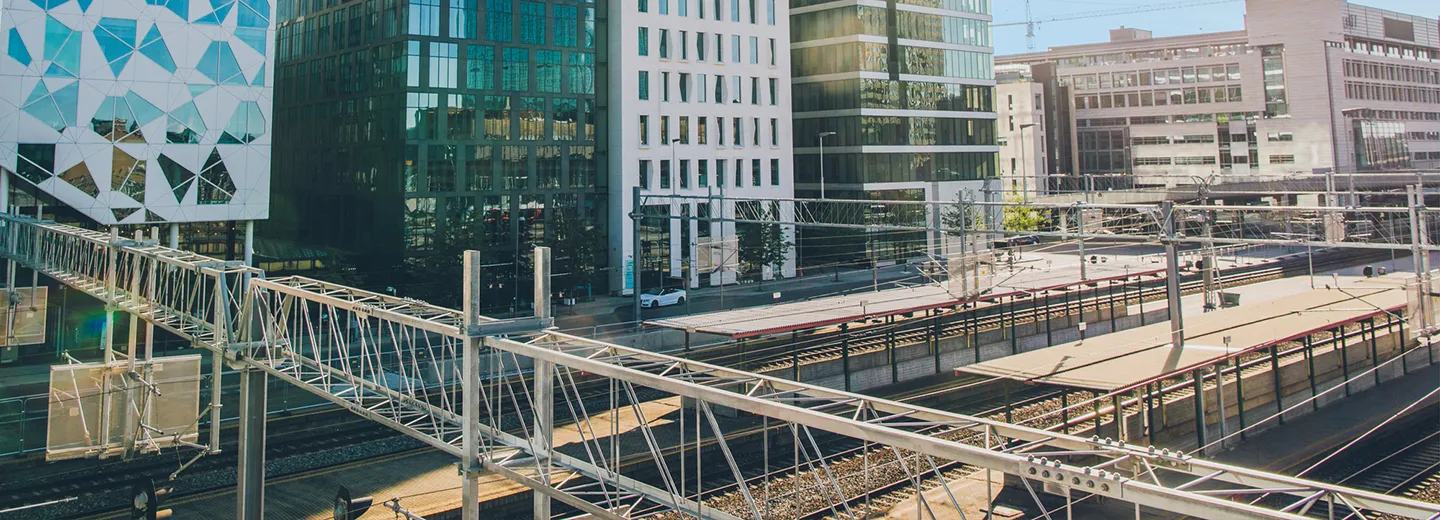
Since 1969, the American Welding Society codes governing structural welding have recognized ultrasonic testing as a method of examining completed welds for defects that would be a cause for rejection. The methodology for these examinations and the acceptance criteria for them is detailed in Clause 6 of AWS D1.1 Structural Welding Code – Steel.
Additionally, AWS D1.8 Seismic Supplement requires that UT technicians who will examine welds in the seismic force resisting system (SFRS) of structures pass a supplemental practical examination requiring the testing of a variety of welds of various configurations and a minimum of 20 known flaws.
The pass/fail criteria show that a technician who correctly locates and characterizes 90% of the rejectable flaws and reports 10% false positives (that is, indicates a rejectable flaw at a location where none exists) will pass the supplemental test.
Now, consider that a welder whose rate of producing welds with no rejectable flaws is 95%. The California Building Code allows a reduction in the percentage of welds in the SFRS required to be nondestructively tested by this welder to be reduced from 100% to 25%, indicating that the code considers such a welder to be producing excellent work.
Finally, consider our UT technician who has passed the supplemental exam in AWS D1.8 with the scores described above. This technician reports a rejectable flaw in a weld by the welder described above. I invite you to estimate the probability that a rejectable flaw actually exists in the weld. As a hint, this is analogous to a situation posed to groups of doctors considering a mammogram that shows positive for a breast tumor. Like the situation with UT, most breasts do not have tumors, most tumors that actually exist are detected, and occasional false positive indications of tumors are found.
The answer, using the methods first detailed by Reverend Thomas Bayes in the 1700s, is 32.1%! A detailed explanation of the calculations is beyond the scope of this blog posts, but I refer the interested reader to the Wikipedia article entitled “Bayesian Inference” for a start.
Admittedly, we’d rather have false positives than false negatives since false negatives can precipitate failure of the weld in service. Still, removal of metal and replacement is costly and time consuming. False positives are far from benign. So how can we reduce the percentage of false positives? One way is to find welders who install welds with many more flaws than 5% but this is probably not optimal! The best way is to provide much more rigorous training and standards to technicians so that their rate of false positive calls is far below the 10% level mentioned above.
At Twining, Inc., we are committed to a continuing program for training and evaluation of our UT technicians to achieve the highest standards of quality and reliability. Training to eliminate false positives while maintaining extremely high probability of detection of actual flaws and the correct characterization of these flaws is central to that program.
Robert M. Ryan has been affiliated with Twining Laboratories and its associated companies since 1977. He brings vast knowledge in all areas of field inspection, and is a leading expert on all aspects of structural steel construction and non-destructive testing. His experience includes oversight of special inspection for some of Southern California’s landmark projects. Mr. Ryan provides consultation on welding and non-destructive procedures, including specification preparation and review, and on complex problems related to welding such as cracking, unusual joint configurations, etc.
Have a question about this post? Ask Rob here: https://twininginc.com/ask-an-expert/